My first time on a “foil ready” board. At first I didn’t get it. There I was on a windsurfing board, holding a super fast racing sail in my hands, ready to take off as I have done thousands of times before. Getting used to that giant foil beneath me took some time.
I got it the second day, partly. The strong winds combined with my determination to learn this had its consequences. The board jumped up and down as I struggled to control the foil and it didn’t like it. It broke. Not in two pieces, but almost. Shit, this needs fixing. How?
Ok, trying to save some money, I went to the hardware store to see if there were alternatives to the West Systems Epoxy. Big mistake.
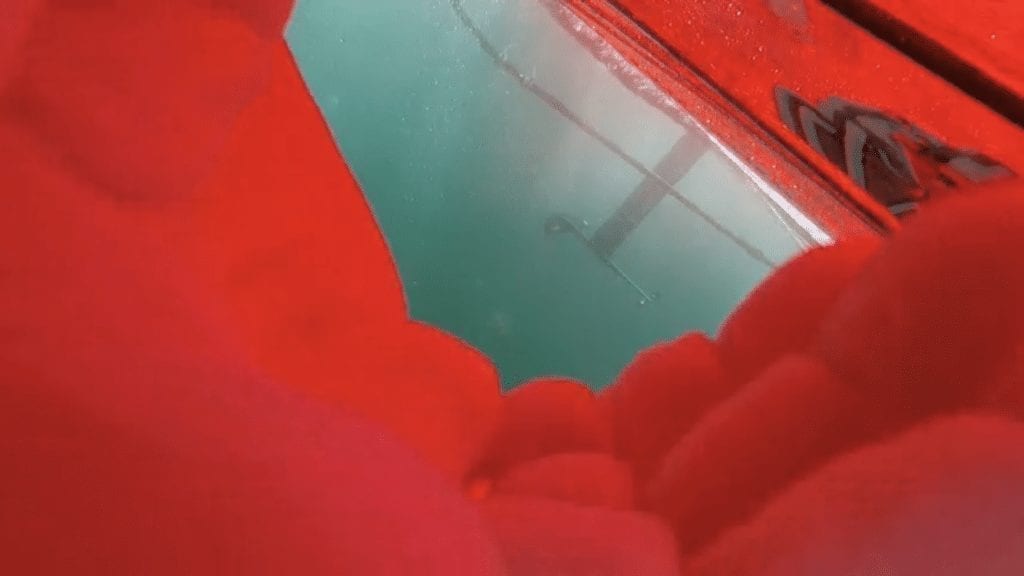
Also read: Foil face plant
First I removed the broken, loose laminate parts. Then I put the board for drying in 3 days. Important. In stead of micro balloons for my filler (didn’t have it), I used icing sugar. This is gonna be fine, I thought to myself. A bit of sanding and two layers of fiber glass on top. The resin I used is made for boats and was grey. Well, as long as it stays, it doesn’t matter.
I used the board the whole summer and thought that everything was good. Then, in August, I discovered water coming out of the repair area. The repaired area started to get soft. Not good. Epoxy is supposed to be hard as rock.
I cut the board open to have a look. F”#¤%##!!! A huge cavity the size of a drawer going through the board?! As if a rat had been feasting.
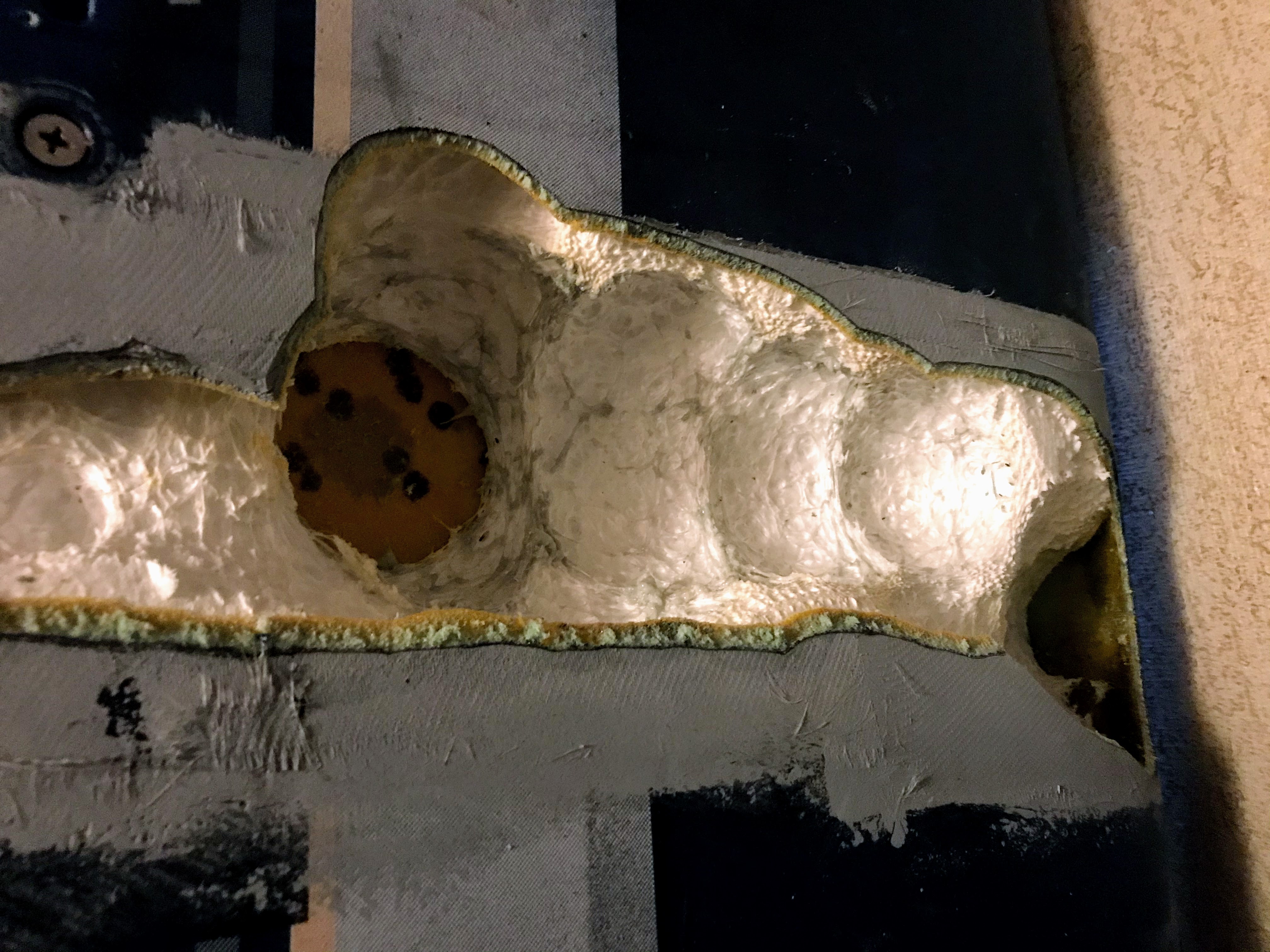
This is what the wrong stuff does with the foam
The fixing solution
Expanding insulation foam. That was my first reaction. I had been using it a few times fixing my windsurfing boards back in the 1990s. I got into the car and drove to the West System store on the other side of the city. One of the guys there understood the crisis when I explained the blunder. – Expanding foam, well, yes, that could work, he nodded. – And the epoxy will not react with the foam?, I asked. The guy called on a colleague. – No, it won’t, he assured me.
– Ok, good. Hand me a West System repair kit, then, I replied. – And thanks for the advice. Next stop, the hardware store to get foam and straight back home.
I put the board back for drying for three days. Completely dry and it was ready for the foam. This is cool, I thought to myself. Really easy to work with. I put it into every nooks and crannies and it expanded perfectly into a hard and light material.
Since the board had almost broken into two pieces I thought a couple of stringers would be a good idea.
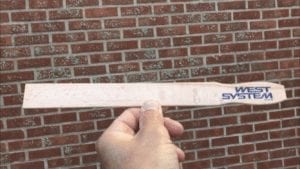
Hm, where do I find rigid wood? I looked around me and saw the spatulas I had bought together with the epoxy. I bent it a few times and decided this could work. Cut it into two 20-30 cm pieces and squeezed them into the foam before it hardened. One stringer on each side. Looked good. Should work.
Then it was time to cut and sand the hardened foam. Super easy. I got a nice surface. Again, I used icing sugar for my filling. Micro balloons makes the best filler, but it’s more expensive. To layers of fiber glass and epoxy. Dry it and sand it. Two days after my daughter and I went out windsurfing.

Also read: Snow canons to save coral reefs